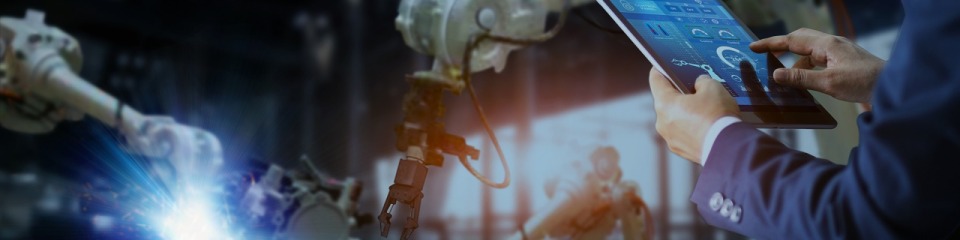
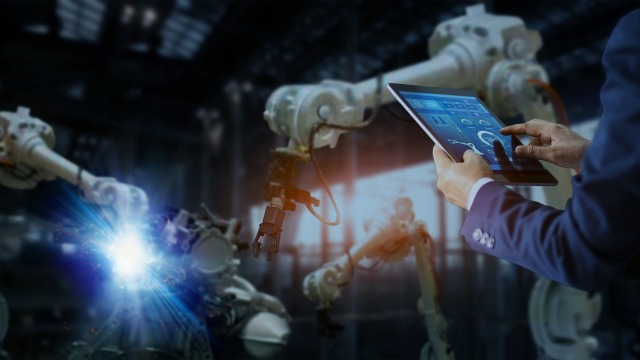
Produkte
ÜbersichtBranchen
ÜbersichtService
ÜbersichtDownloads
ÜbersichtSo kaufen Sie
ÜbersichtUnternehmen
ÜbersichtProduktgruppen
ÜbersichtKonfiguratoren und Tools
ÜbersichtCertified Excellence-Partnerprogramm
ÜbersichtEDI (Electronic Data Interchange)
ÜbersichtWarum braucht eine Schweißsteuerung Industrie 4.0-Fähigkeit? Es ergeben sich beim Schweißen wahre Schätze: immense Datenmengen. Sie können die Basis für Prozessoptimierung, Machine Learning und Wertschöpfung bilden. Dafür müssen sie jedoch zunächst gesammelt, analysiert und weiterverarbeitet werden. Verbreitete Standards, um an diese Daten zu gelangen, sind MQTT und OPC UA. Bosch Rexroth bündelt in dem Paket „IoT Connector“ diese beiden Kommunikationsarten. Anwendende können so die erhobenen Daten nach ihren Bedarfen weiterverarbeiten und beispielsweise automatische Protokollierung zur Qualitätssicherung umsetzen.
Die Schweißsteuerung PRC7000 kann ganz einfach fit für die Industrie 4.0 gemacht werden – und zwar mit dem Paket „IoT Connector“, in dem die beiden Kommunikationsarten MQTT und OPC UA zusammengefasst sind.
Die Steuerung arbeitet als Prozessgerät und Kommunikationsgateway in einem. Der IoT Connector stellt Daten für die Weiterverarbeitung zur Verfügung, beispielsweise für statistische Auswertungen oder dauerhafte Protokollierungen. Ziele sind unter anderem Kosteneinsparungen im Qualitätsmanagement sowie die vorbeugende Wartung. Dies sind zunehmend Prioritäten beim Widerstandsschweißen z. B. in Bereichen der Automobilindustrie beim Karosserie-Rohbau, im Bereich der TIER1-Zulieferer und auch im Maschinenbau.
Beide Kommunikationsarten zählen zu den führenden: MQTT als offenes Netzwerkprotokoll und OPC UA als Kommunikationsstandard in der Automatisierung.
MQTT ist auf Umgebungen mit niedriger Bandbreite und hoher Latenz ausgelegt. Es ist ideal geeignet, um enorme Datenmengen in Päckchen zu versenden. So werden bei einer Steuerung zum Beispiel bis zu 30.000 Schweißpunkte pro Tag gespeichert und verschickt. Die Steuerung PRC7000 versendet die Daten dabei im JSON-Format – ein textbasiertes, selbstbeschreibendes Format, das vom Menschen interpretierbar ist.
OPC UA besitzt die Fähigkeit, Maschinendaten nicht nur zu transportieren, sondern auch maschinenlesbar semantisch zu beschreiben. So können Daten in die Cloud geschickt, analysiert und dann Rückschlüsse in die Steuerung geschrieben werden. Das bildet die Grundlage für Anwendungen in Richtung Machine Learning und Künstlicher Intelligenz (KI).
Beide Standards sind im IoT Connector verfügbar. Als Basisfunktionalität ist neben einem MQTT-Publisher ein OPC UA Server bereits im Standardlieferumfang der Schweißsteuerung PRC7000 enthalten. Der Datenumfang lässt sich durch eine Lizenz erweitern, sodass sich noch mehr Anwendungsfälle ergeben.
Bisherige Schweißsteuerungen waren auf Grund unzureichender Leistungsfähigkeit nicht für die Implementierung von Protokollen wie MQTT und OPC UA ausgelegt. Eine Middleware- bzw. Gateway-Software, die unter Umständen eine eigene Hardware benötigte, musste zwischen Device und Edge- oder Cloud-Layer geschaltet werden. Die Daten wurden von der Middleware abgeholt, aggregiert und abgeschickt.
Der IoT Connector unterstützt die vertikale Integration aus dem Prozessgerät heraus, z. B. in die Cloud oder Edge. Als offenes System unterliegt er keinen proprietären Strukturen und bietet eine state-of-the-art-Kommunikation. Anwendende können die Daten nach ihren Bedürfnissen weiterverarbeiten. Bei der Steuerung PRC7000 ist ein festgelegter Datenumfang – zum Beispiel für die iO/niO-Auswertung – standardmäßig enthalten.
Das erweiternde Paket ermöglicht einen noch umfangreicheren Datenfluss und damit weitere Anwendungsfälle. Mit dem IoT Connector lassen sich zum Beispiel mehr als 200 IST-Werte je Schweißpunkt ermitteln. Dazu zählen Qualitätswerte, Rohdaten von Schweißkurven, diverse Parameter wie Sollwerte, Einstellungen und Referenzkurven sowie Datenänderungen. In Kombination mit der Auswertung weiterer Datenquellen lassen sich vorbeugende Instandhaltungskonzepte realisieren. Weitere Vorteile im Sinne von Transparenz, um Optimierungspotenziale sichtbar zu machen und ausschöpfen zu können: Es kann eine automatische Protokollierung zur Qualitätssicherung umgesetzt werden. Protokollierte Parameteränderungen ermöglichen Analysen der Schweißpunktqualität und der Status im Rohbau lässt sich über Parameterinformationen visualisieren.
In der Industrie ist heute eine flexible und wandlungsfähige Produktion gefragt, die auf sich dynamisch verändernde Anforderungen reagieren kann. Dies erfordert anpassungsfähige Lösungen, die Vernetzung und Durchgängigkeit unterstützen. Bosch Rexroth stellt sich mit dem IoT Connector auf die Bedürfnisse in der modernen Fabrik ein. Damit lassen sich die Schweißsteuerungen PRC7000 und PSI6000 von Bosch Rexroth Industrie 4.0-gerecht erweitern und Datenschätze heben.
Autor: Domenico Livani
Funktion: Produkt Manager Widerstandspunktschweißen, Bosch Rexroth AG