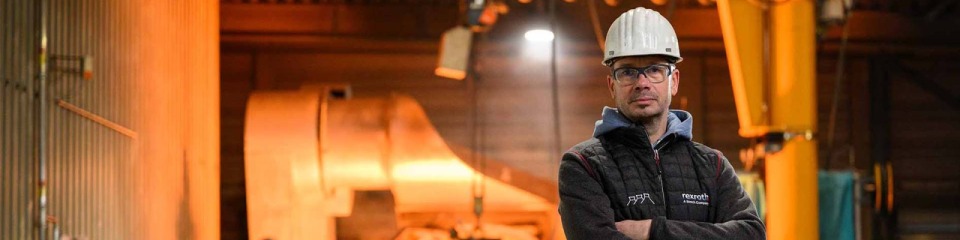
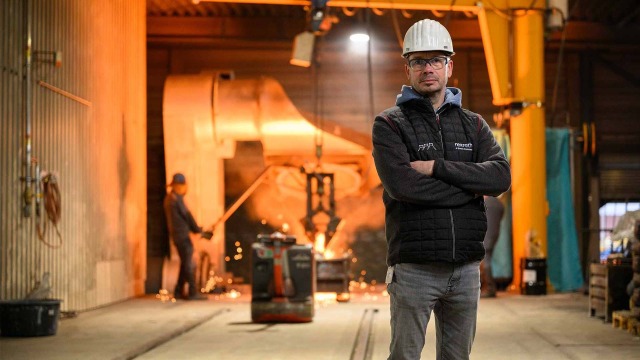
Bei Bosch Rexroth sind wir kontinuierlich auf der Suche nach Möglichkeiten, Energie einzusparen. Erfahren Sie mehr über einige der jüngsten Innovationen, die wir in unseren eigenen Werken implementiert haben. Diese zeigen, wie wir mit kreativem Denken und sorgfältiger Analyse zu einer gesteigerten Energieeffizienz beitragen können.
Neue Wege in der Wärmebehandlung
Im Werk Lohr werden Hydraulikgussteile in verschiedenen Qualitäten hergestellt. Ein Teil dieses Produktionsprozesses beinhaltet eine spezielle Wärmebehandlung, das sogenannte "Glühen", bei der die Gussteile auf über 900 °C erhitzt und anschließend nach genau definierten Vorgaben abgekühlt werden.
Beim Glühen werden große Mengen an Energie verbraucht. Hierbei haben unsere Experten einen energieeffizienteren Weg gefunden, welcher das Glühen im Prozess ersetzt, indem die Kühlung verlangsamt wird.
Durch ein neues Kühlhaus kann auf den Glühprozess verzichtet und somit der Kohlendioxidausstoß unserer Produkte um mehr als 2.500 Tonnen pro Jahr reduziert werden.
(Bildquelle: Bosch Rexroth)
Modernisierung des Schmelzprozesses
In unserer Gießerei in Lohr wurde ein neuer Mittelfrequenzofen installiert. Der neue Ofen verfügt über modernste Schmelztechnologie, welche auf eine gesteigerte Energieeffizienz ausgelegt ist. Dies ermöglicht es, drei bestehende Öfen durch den neuen Mittelfrequenzofen zu ersetzen.
Durch die Digitalisierung und Automatisierung der Schmelzprozesse, die Umstrukturierung des Materialflusses und die Reduzierung des Eisentransports – und damit des daraus resultierenden Temperaturverlustes – können wir unseren Energieverbrauch weiter verringern. Durch den neuen Schmelzbetrieb können wir künftig bis zu 2,9 GWh Energie pro Jahr einsparen.
(Bildquelle: Bosch Rexroth)
Umstellung auf zentrale Wasserkühlung
Kompressionskältesysteme sind ein wichtiger Bestandteil des Produktionsprozesses für Hydraulikkomponenten in unserem Werk in Peking. Diese funktionieren ähnlich wie Kühlschränke oder Klimaanlagen, wobei bei laufender Anlage warme Luft abgegeben wird. Die warme Luft muss über die Lüftungsanlage aus der Halle abgeführt wird. Das bedeutet einen hohen Energieverbrauch.
Unser Team untersuchte, wie das Energiemanagement verbessert werden könnte, und wandte sich dem bestehenden Kaltwassernetz der Anlage zu, das bereits zur Kühlung anderer Maschinen und Prozesse in der Produktion genutzt wird. Sie stellten fest, dass die Energieeffizienz deutlich verbessert werden könnte, indem dieses bestehende Kaltwassernetz zur Kühlung installierter Maschinen genutzt wird. Die Kompressionskälteanlagen konnten durch einen Wärmetauscher ersetzt werden, der an das Kaltwassernetz angeschlossen ist.
In der ersten Phase wurden fünf der Bearbeitungszentren umgerüstet, was zu einer Reduzierung des Energieverbrauchs für die Kühlung um über 80 % im Vergleich zur dezentralen Lösung führte – was einer jährlichen Einsparung von etwa 85.000 kWh entspricht.
(Bildquelle: Bosch Rexroth)
Energie sparen mit UV-Strahlung
In der Leiterplattenfertigung im chinesischen Werk Xi'an werden Kunstharze nun ohne Hitze mittels UV-Strahlen ausgehärtet. Das reduziert den Energieaufwand der Anlage.
Während des Produktionsprozesses werden Leiterplatten (PCBs) mechanisch mit elektronischen Bauteilen bestückt und verlötet. Nach der Funktionsprüfung wird die bestückte Leiterplatte (PCBA) mit einem Lack beschichtet, um die Elektronik vor äußeren Umwelteinflüssen zu schützen. Damit ist er für den Einsatz in industriellen Anwendungen geeignet.
Bis vor Kurzem wurde diese Beschichtung bei einer Temperatur von etwa 100°C für 15-20 Minuten getrocknet. Anschließend mussten die PCBAs zwei Stunden lang abkühlen. Durch den Einsatz der UV-Technologie löste das Produktionsteam innerhalb von Sekunden eine chemische Reaktion aus. Über 80 % des Energieverbrauchs können hierdurch im Vergleich mit dem vorherigen Prozess eingespart und die Trocknungszeit um etwa 90 % verkürzt werden. Darüber hinaus ermöglicht das Verfahren das Auftragen einer dickeren Farbschicht, was zu einem verbesserten Schutz und höherer Qualität der hergestellten Leiterplatten führt.
(Bildquelle: Bosch Rexroth)
Leo Pototzky
Leitung, Operational Sustainability