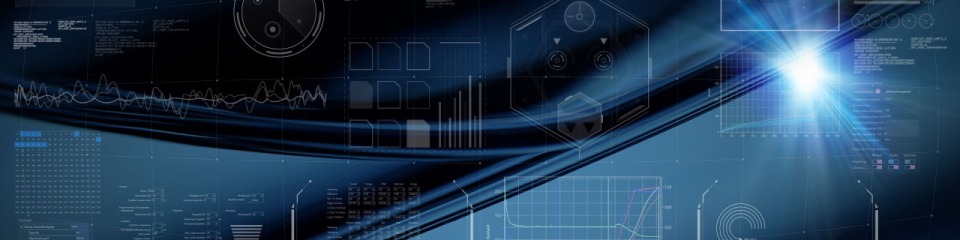
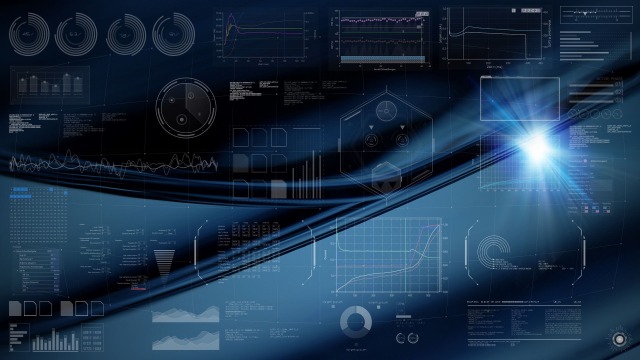
Produkte
ÜbersichtBranchen
ÜbersichtService
ÜbersichtSo kaufen Sie
ÜbersichtUnternehmen
ÜbersichtProduktgruppen
ÜbersichtEngineering
ÜbersichtKonfiguratoren und Tools
ÜbersichtCertified Excellence-Partnerprogramm
ÜbersichtEDI (Electronic Data Interchange)
ÜbersichtEin Fahrzeug soll in vier Varianten gebaut werden – und dies in sechs Werken weltweit, auf acht Produktionslinien. Dabei ergeben sich über 120.000 Schweißpunkte, deren Parameter ermittelt, eingegeben, optimiert und validiert werden müssen. Dieses Beispiel zeigt, wie hoch die Anforderungen an das Widerstandspunktschweißen sind. Und die Komplexität steigt: Mit anhaltenden Trends, wie zum Beispiel Leichtbau, wird das Verfahren in Bezug auf Prozessstabilität und Produktivität immer wieder vor neue Herausforderungen gestellt. Hier ist eine Schweißsteuerung gefragt, die sich zum Beispiel Materialmischungen schnell und dynamisch anpasst.
320 Teile, 80 Blechgüten und Beschichtungen, in verschiedenen Dicken – das ergibt exemplarisch 500 Materialdickenkombinationen, verbunden durch 5.000 Schweißpunkte. So kann heute eine Fahrzeugkarosserie aussehen. Und sie wird immer anspruchsvoller. Denn beim Fahrzeugbau geht der Trend hin zur Entwicklung immer leichterer und sicherer Fahrzeuge. Ein Grund: Ein geringeres Gewicht vermindert zum einen den Treibstoffverbrauch und damit den CO2-Ausstoß, zum anderen senkt der Automobilherstellende durch die Materialeinsparung seine Produktionskosten. Dabei gibt es zunehmend komplexere Formen beim Design und gleichzeitig müssen die Anforderungen an die Crash-Sicherheit eingehalten werden.
Die anspruchsvollen Schweißaufgaben nehmen durch Mischkombinationen von Materialien in unterschiedlichen Varianten weiter zu. Im Automobilsektor werden darüber hinaus immer mehr Fahrzeugvarianten und -modelle über die gleiche Linie gefahren. Dies alles nimmt einen direkten Einfluss auf die Inbetriebnahme und die Anforderungen an Schweißregelung und -überwachung.
Damit die erforderlichen Leichtbaukonzepte umgesetzt werden können, stieg der Einsatz von anti-korrosionsbeschichteten, höchstfesten Stahlwerkstoffen im Fahrzeugbau in den vergangenen Jahren kontinuierlich an. Mittels höchstfester Stähle können Bauteile mit verringerten Wandstärken ausgelegt werden – bei der gleichzeitigen Einhaltung der mechanischen Anforderungen. Diese Werkstoffe weisen jedoch beim Widerstandspunktschweißen in der Regel eine erhöhte Neigung zur Ausbildung von schweißbedingten Rissen auf.
Eine weitere Herausforderung: Beim Widerstandspunktschweißen von Aluminium und Stahl treffen zudem zwei Grenzbereiche der Physik aufeinander. Stahl besitzt einen hohen elektrischen Widerstand, Aluminium dagegen einen geringen Widerstand. Die neue, leistungsstarke Schweißsteuerung PRC7000 von Bosch Rexroth beherrscht beide Grenzbereiche. Hierzu wandeln Transformatoren die Ausgangsleistung der Schweißsteuerung passgenau für die jeweilige Schweißaufgabe um.
Mit der PRC7000 können unterschiedliche Blechdickenkombinationen sowie Materialmischungen – von Stahl bis Aluminium – problemlos verarbeitet werden. Die neue Schweißsteuerungsgeneration bedient sich dafür adaptiver Regler sowie einer flexiblen Programmierbarkeit. Mit der Schweißsteuerung werden zudem perfekte Schweißpunkte reproduzierbar.
So hat beispielsweise ein führendes automobilherstellendes Unternehmen in einem neuen Fahrzeug erstmals in hoher Anzahl das Widerstandspunktschweißen von Aluminiumteilen am Fahrzeugchassis umgesetzt. In diesem Fall besteht die Hauptkarosse aus Aluminium und bringt ca. 2.000 Schweißpunkte mit unterschiedlichen Alublech-Kombinationen mit.
In der neusten Ausbaustufe der PRC7000 bieten z. B. die Zangenspeichermodule die Möglichkeit, die Prozesssignale bereits auf der Zange zu digitalisieren. Handzangen beispielsweise können so an jeder verfügbaren Steuerung betrieben werden, ohne dass die Steuerung dazu neu parametriert werden muss. Die Daten werden in Form einer vollständigen Schweißaufgabe direkt im Zangenspeicher gespeichert und können störgemindert an die Steuerung übermittelt werden. Für Anwendende ergibt sich somit ein breiterer Handlungsspielraum und die Möglichkeit für neue Use-Cases sowie Kosteneinsparungen.
Automobilherstellende können mit der Schweißsteuerung PRC7000 also effizient, flexibel und gleichzeitig nach höchsten Qualitätsmaßstäben die hohen dynamischen Anforderungen im Widerstandspunktschweißen umsetzen. So sind nicht nur Ökonomie, Prozessstabilität und Produktivität, sondern auch Wettbewerbsfähigkeit gewährleistet.