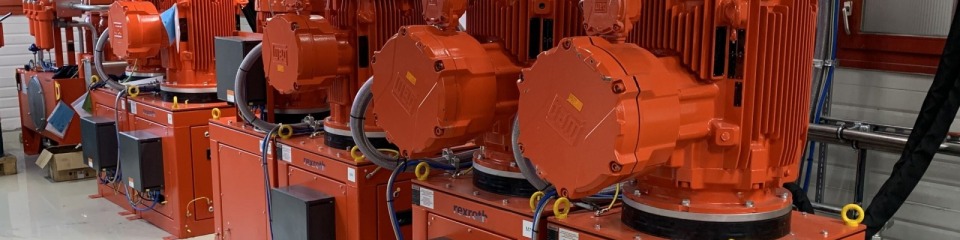
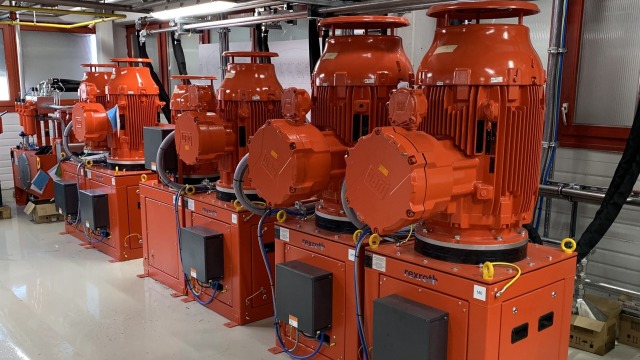
Lange Zeit verbrauchten die mehr als 20 Rührwerke und Mischer, mit denen die Firma Stahl im Werk Leinfelden Grundstoffe für Hochleistungsbeschichtungen herstellt, viel Strom. Dank einer innovativen Hydrauliklösung von Bosch Rexroth arbeitet die Produktionsanlage jetzt um 60 Prozent energieeffizienter. Gleichzeitig profitiert das Unternehmen von einer höheren Prozesssicherheit und -qualität.
Es gibt Produkte, die nur wenige Menschen kennen, obwohl sie aus ihrem Alltag nicht wegzudenken sind. Solche Hidden Champions sind zum Beispiel Hochleistungsbeschichtungen für Schuhe, Kleidung, Heimtextilien oder die Innenausstattung von Autos. Als weltweit führend auf dem Gebiet dieser Performance Coatings gilt die Firma Stahl, die in ihrem Werk in Leinfelden bei Stuttgart hunderte von Rezepturen herstellt.
Das Gelingen der sensiblen Reaktions-, Misch- und Dispergierprozesse hängt unmittelbar von der Drehzahl der Hydraulikmotoren ab, die an den insgesamt 23 Rührwerken der Anlage montiert sind. Je nach Prozessschritt müssen die hydraulischen Antriebe über weite Strecken ein möglichst konstantes Wellendrehmoment, zeitweise aber auch ein deutlich höheres Kraftniveau erzeugen. Um den Normalbetrieb und die vereinzelten Leistungsspitzen möglichst energieeffizient abzubilden, beauftragte Stahl Bosch Rexroth mit der Modernisierung der Hydraulik.
Hochleistungsbeschichtungen verleihen unter anderem Schuhen besondere Eigenschaften. (Bildquelle: Stahl)
Konkreter Anlass für die Entwicklung des neuen Antriebskonzepts war die Einstellung der Produktion des bisherigen Hydromotorenherstellers, wodurch letztlich auch die Ersatzteilversorgung gefährdet war. Auf der Suche nach einer Alternative wandte sich Stahl an den regionalen Anbieter Hydrobar aus Sindelfingen, der zum Certified Excellence-Partnernetzwerk von Bosch Rexroth gehört. Aufgrund der komplexen Anforderungen empfahl Hydrobar, die Anfrage direkt an den Rexroth-Geschäftsbereich Hägglunds zu richten.
Neben den Hydromotoren sollte auch die bisherige Zentralversorgung im laufenden Betrieb schrittweise durch ein effizienteres Antriebskonzept ersetzt werden. „Uns war aufgefallen, dass der Stromverbrauch der Anlage nicht mit der Auslastung korrelierte“, berichtet Miquel Forcadell, Projektleiter bei Stahl in Leinfelden. „Entsprechende Verbrauchsmessungen ergaben ein Einsparpotenzial von über 60 Prozent, was auf das gesamte Werk bezogen einer Energieeinsparung von rund 15 Prozent entspricht. Diese Einsparung bei den größten Verbrauchern unseres Standortes war die Vorgabe für das Projekt.“
Meilenstein der ESG-Strategie: Der Stahl-Standort Leinfelden spart durch das neue Hydraulikkonzept von Bosch Rexroth insgesamt 15 Prozent an Strom und CO2-Emissionen ein. (Bildquelle: Stahl)
Verantwortlich für die große Diskrepanz zwischen erzeugter und tatsächlich benötigter Energie war die vorhandene zentrale Energieversorgung, deren Kapazität ursprünglich nur für sieben Rührwerke ausgelegt war. Die elektrisch angetriebenen Hydraulikpumpen erzeugten einen konstant hohen Druck, der permanent viel Strom verbrauchte. Abgesehen von gelegentlichen Leistungsspitzen wurde das System durch Ventile gedrosselt, so dass ein Großteil der hydraulischen Energie in Wärme umgewandelt wurde.
„Im Rahmen unserer ESG-Strategie arbeiten wir kontinuierlich daran, Großverbraucher zu identifizieren und ihren Energiebedarf zu optimieren“, erklärt Standortleiter Salvatore Alfieri. Außerdem wollte Stahl mit dem Modernisierungsprojekt die Produktionsprozesse transparent und besser steuerbar machen. Durch die Erfassung und Bereitstellung aller Antriebsdaten an die übergeordnete Steuerung, können Prozesse in Zukunft weiter optimiert werden.
Doch die Anforderungen an das Projekt waren noch komplexer: Neben den Nachhaltigkeits- und Digitalisierungszielen sollte Bosch Rexroth ein Antriebskonzept entwickeln, das neben den bedarfsabhängigen Rührvorgängen auch die Arbeitsbedingungen in unterschiedlichen ATEX-Zonen berücksichtigt. Zudem musste das neue Hydrauliksystem bei laufender Produktion installiert und in Betrieb genommen werden. Bosch Rexroth erfüllte diese komplexen Anforderungen mit einem maßgeschneiderten Konzept, übernahm die Projektierung und lieferte unter anderem neun Radialkolbenmotoren der Hägglunds Baureihe AMX für die langsam laufenden Hochmoment-Reaktoren. Diese sind im Vergleich zur bisherigen Lösung deutlich kompakter und leistungsstärker. Darüber hinaus wurde die Ölversorgung für alle 23 Antriebe durch neue Kompaktaggregate ersetzt, wobei alle Hochdruckmodule mit drehzahlgeregelten Pumpen betrieben werden.
Von den beiden zentralen Einspeiseeinheiten ist jeweils eine Pumpeneinheit redundant ausgeführt. Da sich einer der beiden Maschinenräume im Ex-Bereich befindet, wurden die dort installierten Kompaktaggregate in ATEX-Ausführung realisiert. Für die präzise Steuerung der drehzahlvariablen Hydraulikantriebe kommen Rexroth Frequenzumrichter zum Einsatz. Certified Excellence Partner Hydrobar sorgte für die exakte Verrohrung der Anlage und stellt die Wartung sicher.
Aus Sicht von Stahl war das Engineered-to-Order-Projekt ein voller Erfolg. In nur fünf Monaten gelang es Bosch Rexroth und den für die verschiedenen Gewerke beauftragten Partnern, die Hydromotoren und drehzahlvariablen Antriebe auszutauschen. „Nach der Vorbereitung der Verrohrung und Elektrik inklusive der Frequenzumrichter wurde das betroffene Rührwerk in der produktionsfreien Zeit am Wochenende vom bestehenden Konstantdrucknetz getrennt“, beschreibt Projektleiter Forcadell das schrittweise Vorgehen. „Die modernisierten Rührwerke konnten in der Regel nach drei Tagen wieder in Betrieb genommen werden.“
Für eine termingerechte Umsetzung unterstützte Bosch Rexroth das Montageteam nach Bedarf auch bei der Installation der neuen Hydraulikmotoren und der Kompaktaggregate. „Trotz seiner Komplexität wurde das Projekt sehr schnell umgesetzt, insbesondere auf der Steuerungsseite. Die Verrohrung durch Hydrobar war vorbildlich. Jede Anlage wurde sehr gut vorbereitet, getestet und immer schneller schlüsselfertig übergeben. Die letzten sechs Antriebe waren innerhalb einer Woche ausgetauscht.”
Von diesem Schaltschrank aus steuern die Umrichter die drehzahlvariabel angetriebenen Rexroth Kompaktaggregate zur Fluidversorgung der Hydromotoren. (Bildquelle: Stahl)
Auch die geplanten Energieeinsparungen konnten in vollem Umfang realisiert werden. „Das Multitechnologie-Projekt von Bosch Rexroth war ein weiterer Meilenstein in unserer ESG-Roadmap“, sagt Alfieri. „Die tatsächliche Einsparung im Vergleich zum alten Konstantdrucksystem beträgt 60 Prozent, wodurch das gesamte Werk insgesamt 15 Prozent weniger Strom verbraucht. Durch den drehzahlvariablen Ansatz zur bedarfsgerechten Stromversorgung bleibt der absolute Stromverbrauch auf einem konstant niedrigen Niveau. Auch bei einer hohen Auslastung der Rührwerke treten keine Schwankungen mehr auf, so dass die Prozesssicherheit durchgehend gewährleistet ist.“
„Da die moderne Steuerung für jeden Prozessschritt genau die benötigte Leistung bereitstellt, können wir die Rührbedingungen jederzeit unter Kontrolle halten“, ergänzt Projektleiter Forcadell. „Auf diese Weise profitieren wir bei optimaler Energieeffizienz von einer hohen Reproduzierbarkeit des Produktionsprozesses und einer konstanten Qualität unserer Produkte.“ Auch mit der Stabilität ist Forcadell zufrieden. „Die Dimensionierung der kompakten Aggregate mit einer redundanten Pumpe ist genau richtig. Bis heute gab es keinen einzigen Stillstand.“
Leicht und leistungsstark: Der neue Hägglunds AMX Radialkolbenmotor (rechts) deutlich kompakter als der vorherige Hydromotor (links).(Bildquelle: Stahl)
Durch die neue digitale Steuerung der hydraulischen Antriebe stehen Stahl nun zahlreiche digitale Informationen zur Analyse und Dokumentation der Produktionsprozesse zur Verfügung. „Wir bauen gerade ein Prozessleitsystem auf, um alle Parameter zu visualisieren“, erklärt Alfieri. „Bisher personengebundenes Wissen wird so übertragbar. Die gewonnenen Informationen über bestimmte Einstellungen und schnelle Fehleranalysen vereinfachen die Produktion nachhaltig.“
Durch die digital gesteuerte Hydraulik von Bosch Rexroth kann Stahl die Prozessqualität nun gezielt über die Drehzahl optimieren. Ein willkommener Nebeneffekt der Modernisierung ist zudem der deutlich leisere Betrieb der neuen Hägglunds Hydromotoren und der Kompaktaggregate in den Maschinenräumen. Benötigt das angeschlossene Rührwerk keine Leistung, wird das zuständige Hochdruck-Aggregat komplett abgeschaltet. In der zentralen Serviceeinheit werden automatisch Speisepumpen bedarfsgerecht zugeschaltet. Dieser Standby-Betrieb reduziert zugleich den Geräuschpegel und den Energiebedarf.
Nach der gelungenen Modernisierung der Hydraulikantriebe ist für die Produktionsverantwortlichen am Stahl Standort Leinfelden eine neue Ära angebrochen. „Das Sustainability- und Digitalisierungsprojekt hat die Stabilität und Prozesstransparenz im Bereich Hochleistungsbeschichtungen nachhaltig gesteigert“, resümiert Alfieri. „Es war kein einfaches Projekt, aber die Leistung und Zusammenarbeit von Bosch Rexroth und den beteiligten Partnern war exzellent. Alle Anforderungen wurden innerhalb der geplanten Zeit und des vorgegebenen Budgets realisiert.“