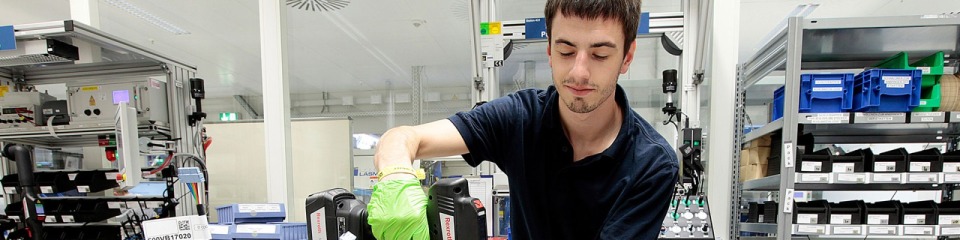
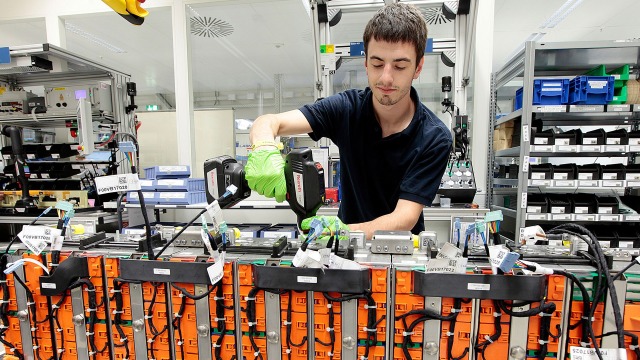
Zuverlässige und effiziente Verschraubung von Batteriepacks für Elektrofahrzeuge
Batteriepacks für Elektro- und Hybridfahrzeuge müssen unter Strom verschraubt werden. Da Montagefehler die Gesundheit der Arbeiter sowie die Funktion und das Sicherheitssystem der Fahrzeuge gefährden, müssen strenge Überwachungs- und Dokumentationsvorschriften eingehalten werden. Welche Lösungen bietet Industrie 4.0 für die normgerechte und zugleich wirtschaftliche Verschraubung von Anschlüssen in Produktion und Service?
Die E-Mobilität nimmt langsam aber sicher Fahrt auf. Schätzungen zufolge sollen im Jahr 2025 fast 20 Millionen Elektro- und Hybridfahrzeuge produziert werden. Produktions- und Serviceleiter sind aufgerufen, Fertigungslinien und Werkstätten entsprechend vorzubereiten. In den kommenden Jahren werden unzählige Batteriepacks je nach Modell mit mehreren Hundert Schrauben montiert und die Leistung, Reichweite und Lebensdauer – vor allem auch die Fahrzeugsicherheit – stark beeinflussen. Wenn einzelne Komponenten während der Fahrt ausfallen, besteht Gefahr für Leib und Leben ebenso wie für die Umwelt. Deshalb schreibt die VDI/VDE-Norm 2862 vor, dass Zulieferer und OEMs jede einzelne sicherheitskritische Schraubverbindung genauestens überwachen und die dokumentierten Daten zehn Jahre lang aufbewahren müssen. Viele Manager fragen sich, wie sie die Umstellung in Produktion und Service kostengünstig und effizient vornehmen und zugleich die Prozessqualität sicherstellen können.
Sicherheitskritische Verschraubung bei der komplexen Batteriemontage: Im Bamberger Bosch-Werk hilft ein intelligenter Funk-Akkuschrauber mit integrierten Sensoren, teure Nacharbeiten, Verletzungen und Produkthaftungsrisiken zu vermeiden.
Ein Batteriepack ist ein komplexes System aus Steuerung, Gehäuseteilen und zahlreichen Batteriemodulen aus Lithium-Ionen-Zellen, die vom Hersteller teilgeladen angeliefert werden. Auch Reparaturen – wie der Austausch eines Moduls – werden normalerweise unter Strom durchgeführt. Ein Kurzschluss bei 400 bis 600 Volt kann tödlich sein. Bei handgeführten Schraubwerkzeugen mit Netzkabelanschluss besteht die Gefahr, dass elektrische Spannung über leitende Metallteile von der Mutter zum Schrauber und von dort aus weiter an die Steuerung übertragen wird. Das ist natürlich auch mit einem erheblichen Risiko für den Bediener verbunden, der den Handschrauber hält und benutzt. Um Verletzungen, Umweltschäden und Produkthaftungsfälle zu vermeiden, ohne die Rentabilität zu gefährden, werden zuverlässige, intelligente und skalierbare Schraublösungen benötigt, die Daten drahtlos erfassen und übertragen können.
Eine solche Komplettlösung, mit der Zulieferer und OEMs mühelos die VDI/VDE 2862-Anforderungen erfüllen und dabei den Bedienern ein Höchstmaß an Sicherheit bieten können, wurde mehrere Jahre lang bei Bosch Rexroth in der Batteriefertigung getestet und schließlich auf dem Markt eingeführt. Sie kombiniert einen vollständig isolierten Nexo Funk-Akkuschrauber mit der speziell für die Batteriemontage konzipierten Schutzisolierung NXAP030/ NXPP012 und verhindert damit nicht nur ein versehentliches Aufsetzen des Schraubers auf spannungsführende Teile der Batterie, sondern auch eine Spannungsübertragung an den Schrauber. Das Design der Schutzisolierung in der Stromklasse bis 800 V ist von der Dekra geprüft. Zudem sorgt die Schutzisolierung dafür, dass sich keine lose Kleidung im Abtrieb verfangen kann.
Die Schutzisolierung für den Abtrieb und die Werkzeugaufnahme schützt den Bediener vor gefährlicher Spannung: Bei der Montage von Batterien für Elektrofahrzeuge können Spannungen von 400 Volt und mehr auftreten, doch bereits bei 48 Volt sollten Vorsichtsmaßnahmen getroffen werden.
Rexroth hat über 30 Jahre technische Kompetenz im Bereich der gesteuerten Schraubtechnik in seinen intelligenten Nexo Funk-Akkuschrauber gepackt. 1982 stellte das Unternehmen das weltweit erste elektrische Schraubsystem mit elektronischer Drehzahlabschaltung vor. In den nächsten zehn Jahren folgten das erste Schraubsystem mit flexibler Schrittprogrammierung und das erste vollständig digitale Schraubsystem. Genau 20 Jahre vor dem Nexo kam der weltweit erste digitale Handschrauber auf den Markt. Die Mehrkanalfähigkeit und die integrierte Logik dieser innovativen Technologie haben bis heute Bestand. Jüngster Meilenstein ist der Process Quality Manager, eine gemeinsam von Bosch Rexroth und Bosch Software Innovations entwickelte Softwarelösung, die mittels Big-Data-Analyse Abweichungen in Produktionsprozessen erkennt.
Richtungsweisende Impulse: Seit 35 Jahren prägt Bosch Rexroth die Entwicklung der gesteuerten Schraubtechnik.
Als Leitanwender bringt Rexroth auch seineIndustrie 4.0-Kompetenz ein. Mit seinem vollständig integrierten Steuergerät fügt sich der Nexo ohne zusätzliche Hardware in das Netzwerk der Fertigungshalle ein und kommuniziert direkt mit dem Liniensteuerungs- und Archivserver. Die webbasierte Software bietet ortsunabhängigen Zugriff auf die Daten – auf einem PC ebenso wie mit einem Smartphone oder Tablet. Dank integriertem Barcodescanner kann der Funk-Akkuschrauber zudem die zusammengehörigen Teile identifizieren und den Bediener präzise durch den Montagevorgang führen. Wenn die Funkverbindung einmal abbricht, speichert das Gerät die Schraubergebnisdaten vorübergehend in einem Datenpuffer und überträgt sie automatisch, sobald die Verbindung wieder hergestellt ist. Mit dezentraler Intelligenz, Konnektivität, integrierter Datenerfassung und gezielter Prozesssteuerung bis Stückzahl 1 erfüllt der Nexo Funk-Akkuschrauber sämtliche Industrie 4.0-Kriterien.
Um den Überwachungs- und Dokumentationspflichten für sicherheitskritische Verschraubungen gerecht zu werden, müssen Drehmoment und Drehwinkel direkt am Akkuschrauber gemessen werden. Dafür können beispielsweise Drehwinkel- und Drehmomentsensoren verwendet werden. Eine indirekte Messung anhand des Strombedarfs genügt den Anforderungen nicht. Die umfangreiche Sensorik des Nexo generiert bei jedem Schraubvorgang bis zu vier DIN-A4-Seiten an Daten, die im Open-Source-Format JSON (JavaScript Object Notation) bereitgestellt werden. Der Prozessmanager erhält eine genaue Grafik, die eine rasche Analyse jedes einzelnen Schraubfalls ermöglicht. Durch den Vergleich dieser Grafik mit dem optimalen Prozess lassen sich weit mehr Montagefehler erkennen, als gesetzlich vorgeschrieben sind. So können während der Batteriemontage beispielsweise beim Anziehen der Kabelschelle anhand vordefinierter Parameter im Schraubprogramm falsche Kabel erkannt werden. Ähnliches gilt auch für falsche Schrauben und fehlende oder doppelte Unterlegscheiben.
Effizienter Ein- und Umstieg: Als skalierbare Gesamtlösung mit integrierter Intelligenz fügt sich der Nexo Funk-Akkuschrauber in vorhandene IT-Systeme ein.
Von der Größe der Datenbank hängt auch ab, wie wirksam eine Fehlervermeidungsstrategie tatsächlich ist und wie effektiv teure Nacharbeiten verhindert werden können. Letztlich folgt die Batteriemontage einem genau definierten Ablauf, der fehlende oder fehlerhafte Schraubverbindungen ausschließt. Um die Anzahl der Schraubverbindungen im Prozess zu kontrollieren und sicherzustellen, dass fehlerhafte Verbindungen (NOK) sofort erkannt werden, kann für jeden Schraubfall ein eigenes Programm erstellt werden, das – einschließlich Lösen und Nachziehen – wiederum in bis zu 12 Schritte unterteilt ist. Eine Displayanzeige und eine Lokalisierungslösung sorgen für präzise Bedienerführung. Die jeweils nächste Schraubstelle wird beispielsweise durch einen blauen Punkt auf dem Monitor angezeigt, der grün wird, sobald der Bediener die betreffende Schraube festgezogen hat. Der Schraubvorgang kann auch problemlos unterbrochen werden. In diesem Fall wird die entsprechende Schraubstelle gespeichert und dem Bediener angezeigt, sobald er die Arbeit wieder aufnimmt. Solange der Schrauber nicht korrekt positioniert ist, wird keine Freigabe erteilt. Eine entsprechende Lokalisierung des Schraubers kann durch Triangulation zwischen Sender und Empfänger mittels Kameratechnik und/oder Ultraschall erfolgen. Bei stationären Systemen lässt sich der Schrauber so bis auf 10 mm genau lokalisieren.
Mit intelligenten Komplettsystemen für die zuverlässige Verschraubung können Automobilhersteller, Zulieferer und Dienstleister die Gesundheit ihrer Mitarbeiter wirksam schützen, die Produktivität über die Überwachungs- und Dokumentationspflichten hinaus steigern und auf lange Sicht die Prozessqualität sichern und optimieren. Darüber hinaus lassen sich die komplexen Abläufe bei der Montage von Batteriepacks für elektrische Fahrzeuge nicht nur normgerecht, sondern auch effizient und fehlerfrei gestalten.