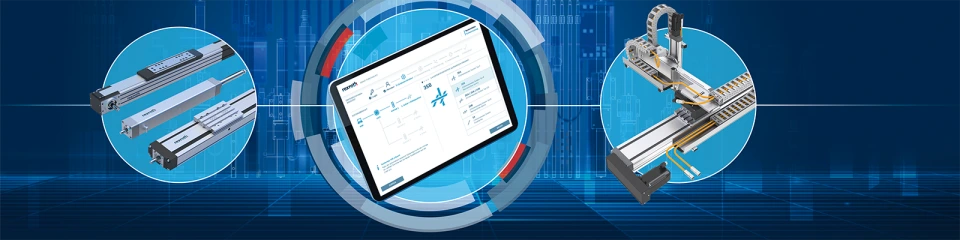
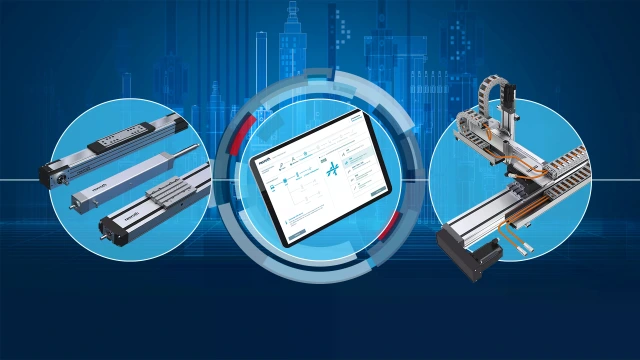
Reducing CO2 emissions, securing the supply chain, absorbing the impact of the shortage of skilled workers: the mechanical engineering sector is facing multiple challenges. Who still has the time to select linear motion technology components from catalogs, dimension them, and coordinate them?
With an intelligently linked portfolio, whose components can be digitally combined to form single axes, actuators, and multi-axis systems, automation is much more efficient and less prone to errors. Especially when the assembled linear axes with automation package is supplemented with motors and drive controllers on request or supplied as a complete subsystem with pre-installed operating software. Automated commissioning and simple visual programming speed up the implementation of automation solutions even more. In this blog post, you will learn how typical single-axis and multi-axis applications in factory automation can be realized quickly and easily.
The range of applications for Linear Motion Technology is expansive: it covers processes such as pick and place, feeding and distributing, as well as placement, separating and stacking, all the way through to assembly, screwing or testing. However, due to the various motion requirements, different linear axes and individual configurations are required for each application. Four typical cases are described below:
Actuators in the form of electromechanical cylinders (EMCs) make a further contribution to efficient factory automation. Compared to pneumatic actuators, they are generally more energy-efficient, low-maintenance, and controllable, as the screw drive directly converts the engine torque into motion. The EMC and EMC-HP Rexroth series, with their ball and planetary screw assemblies in roughly 3,000 different variants, open a wide range of applications for pressing and automation in industries such as electronics and battery production through to automation solutions for fast moving consumer goods (FMCG).
With the optional drive and automation packages from Bosch Rexroth, dynamic positioning tasks with forces from 0.1 kN can be implemented just as easily as pressing and joining applications with up to 250 kN. The Smart Function Kit Pressing also includes an optional force sensor and an industrial PC with pre-installed operating software. As a result, ready-to-operate servo presses can be configured and ordered directly under a material number with just a few clicks.
The browser-based operating software shortens commissioning to a few minutes, programming is done graphically via sequence modules, whereby plausibility checks prevent the system limits from being exceeded. The Smart Function Kit Pressing can easily be connected to a higher-level controller in the place of use by means of prepared function blocks. From there, the servo press can be commanded, and result and process data can be transmitted to the press by the higher-level controller.
Whether single axis, multi-axis system or electromechanical cylinder: With the modular drive and automation packages for linear systems and actuators, a wide range of automation tasks can be solved easily, quickly, and cost-effectively – including complete servo presses and linear robots. In the interest of maximum flexibility, the user decides the desired degree of implementation themselves. For example, single-axis or multi-axis systems can be configured step by step as mechanical or electromechanical systems or to form a complete linear system including control software. In any case, mechanical and plant engineering can make good use of the time gained for other tasks.
Are you interested in even more practical inspiration for modern automation with Linear Motion Technology? Check out the recording here.
Contact our experts for more information and support about the tools and applications.