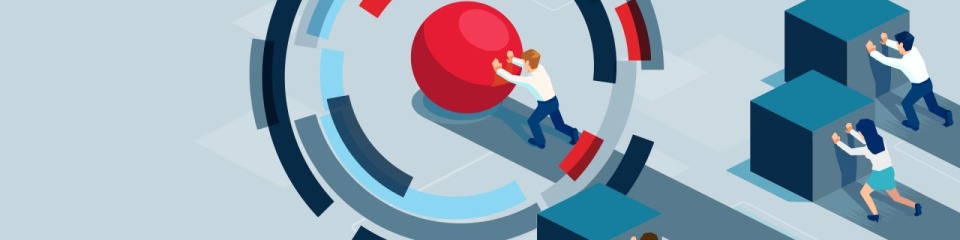
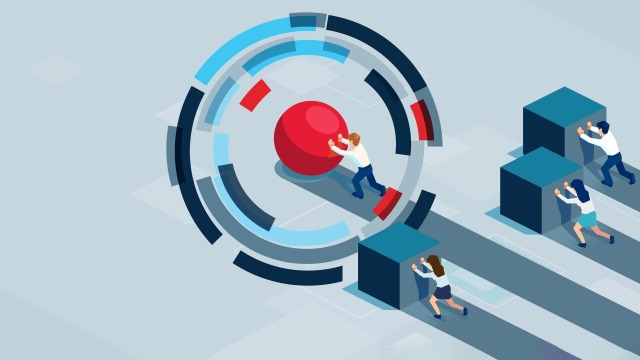
Select your location
Bosch Rexroth around the world
Asia & Pacific
Europe
Never before has efficiency been so vital in manufacturing – especially when businesses around the world are feeling the squeeze. After all, efficiency has a direct impact on profit and can help make your company more competitive. The good news is there are simple ways to make sure your business doesn’t lose out to inefficiencies. Here are some practical tips to help your plant become more streamlined, more effective and better able to adapt in today’s changing world.
The set-up and fine-tuning of equipment takes time and resource. Even though these are planned stops, reducing set-up times can make a significant difference to efficiency without impacting on quality.
Efficiency tip
Innovative software solutions can reduce commissioning times and help you get up-and-running quickly and easily. As an example, our hydraulic power unit, CytroBox, has a commissioning wizard that guides the user through the installation process step-by-step. Meanwhile, our Smart Function Kits are delivered pre-assembled and can be put into operation quickly thanks to the intuitive pre-installed software. This significantly reduces engineering and commissioning times.
Breakdowns and the resulting downtime are a serious issue for manufacturers. They can mean huge revenue losses and disappointed customers, not to mention the inconvenience and the man-hours required to resolve the problem.
Efficiency tip
Get ahead of potential breakdowns and identify them before they even occur with predictive maintenance and a reliable service provider. With our predictive maintenance solutions, data is collected from your system with sensor technology, pre-processed and transferred to the cloud in encrypted form. There, it’s evaluated via algorithms and compared with values from the data pool. In the event of extensive anomalies, a Bosch Rexroth expert steps in and carries out a detailed analysis, informs the user immediately and makes a maintenance recommendation. Maintenance can thus be planned and carried out more efficiently. Rexroth Service includes a rapid and reliable delivery of spare parts, built to original standards and fitted by designated on-site specialists. We can also modernize and network your existing equipment to help increase performance, productivity and energy efficiency.
There are various reasons equipment might run slower than the Ideal Cycle Time (the fastest theoretical time it could take to manufacture an item). It could be that the equipment is dirty or worn out, there could be poor lubrication, substandard materials or poor environmental conditions. If your operators aren’t working in the most efficient way, this will also lead to reduced speed.
Efficiency tip
Monitoring your machines and systems can help to ensure that they’re running at the optimum speed. We can do this as part of a Rexroth Service agreement. When it comes to optimizing human labor, MTM (Methods-Time-Measurement) can be implemented to assess the process, identify activities that can be adapted to improve efficiency and enhance the ergonomics of the workplace to make it more efficient. A trained observer can assess all the activities within the process and break them down into basic motions, independent of the individual employee. This uncovers inefficient activities: maybe the worker has to bend down to pick up the parts or a container has to be moved. Once the workplace and process is optimally designed, it can contribute to long-term efficiency gains, while also providing a more ergonomically beneficial environment for workers.
From starting up your equipment to stable production, there will be defective products that crop up along the way. They can occur after any equipment start-up, but you’re more likely to notice them when you introduce new equipment or machinery to your line.
Efficiency tip
Discover the potential pitfalls in advance with a digital twin – a virtual representation or model of the physical assets in a real factory. We use harmonized and standardized information models and interfaces (APIs) to create an interoperable environment of interconnected components. Once installed, our digital twin solution shows how the different components in a production process work together. This enables you to validate concepts and test processes and procedures before implementing them, which saves valuable time and makes the process more efficient.
Defective parts are often produced during stable or steady-state production. Production rejects do include parts that can be reworked, but this still requires additional effort and impacts efficiency and cost.
Efficiency tip
One way to reduce production rejects is to automate the production process, which can help to make the output more consistent. Another option is to connect and closely monitor machinery in real-time, in order to detect deviations that might lead to production rejects. Our ACTIVE Cockpit provides clear information on machine status in real-time. It gives people on the shop floor access to the data in a format that’s clear and transparent. Technical errors can then be identified and resolved before they cause a problem.