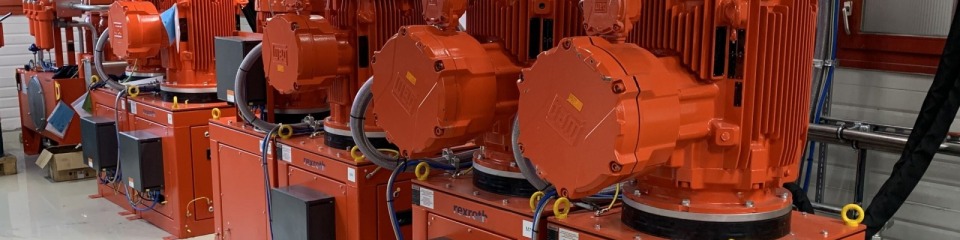
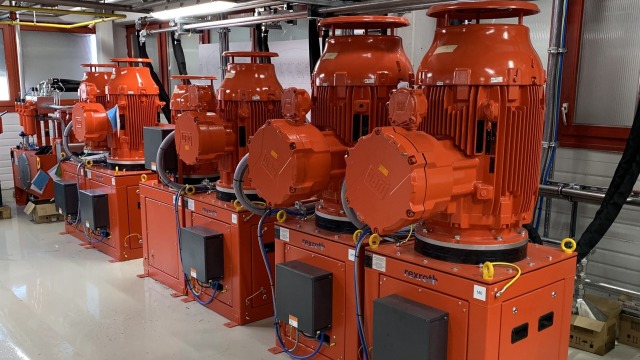
For a long time, the more than 20 agitators and mixers used by Stahl to produce raw materials for high-performance coatings at the Leinfelden plant consumed a lot of electricity. Thanks to an innovative hydraulics solution from Bosch Rexroth, the manufacturing plant is now 60 percent more energy efficient. At the same time, the company benefits from higher process reliability and quality.
There are products that only a small number of people are aware of, even though they are indispensable to our everyday lives. Such hidden champions include high-performance coatings for shoes, clothing, home textiles or car interiors. Stahl, which manufactures hundreds of recipes at its plant in Leinfelden near Stuttgart, is considered to be a global leader in the field of these performance coatings.
The success of the sensitive reaction, mixing, and dispersing processes depends directly on the speed of the hydraulic motors, which are mounted on the plant’s 23 agitators. Depending on the process step, the hydraulic drives must create a shaft torque that is as constant as possible over long distances, but also a significantly higher force level at times. In order to map normal operation and the isolated power peaks as energy-efficiently as possible, Stahl commissioned Bosch Rexroth to modernize the hydraulics.
High-performance coatings give special characteristics to shoes, among other things. (Image source: Stahl)
The development of the new drive concept was prompted by the previous hydraulic motor manufacturer’s discontinued production, which ultimately put the supply of spare parts at risk. In the search for an alternative, Stahl turned to the regional supplier Hydrobar from Sindelfingen, which is part of the Bosch Rexroth Certified Excellence partner network. Due to the complex requirements, Hydrobar recommended that the request be directed directly to the Rexroth Hägglunds division.
In addition to the hydraulic motors, the current central supply is also to be gradually replaced by a more efficient drive concept during operation. “We noticed that the plant’s power consumption did not correlate with the utilization,” reports Miquel Forcadell, project manager at Stahl in Leinfelden. “Relevant consumption measurements showed a potential saving of over 60 percent, which corresponds to an energy saving of around 15 percent for the entire plant. This saving for the largest consumers at our location was the specification for the project.”
Milestone in the ESG strategy: Stahl’s location in Leinfelden saves a total of 15 percent in electricity and CO2 emissions thanks to the new hydraulic concept from Bosch Rexroth. (Image source: Stahl)
The major discrepancy between the energy generated and the energy actually required was due to the existing central energy supply, whose capacity was originally designed for just seven agitators. The electrically driven hydraulic pumps generated a constantly high pressure, which permanently consumed a lot of electricity. Apart from occasional power peaks, the system was throttled by valves, so the majority of the hydraulic energy was converted into heat.
“As part of our ESG strategy, we are continuously working to identify major consumers and optimize their energy requirements,” explains site manager Salvatore Alfieri. With the modernization project, Stahl also wanted to make its manufacturing processes more transparent and controllable. Processes can be improved further in the future thanks to the collection of all drive data and provision to the higher-level control system.
However, the requirements for the project were even more complex: in addition to the sustainability and digitalization goals, Bosch Rexroth was to develop a drive concept that took into account the working conditions in different ATEX zones as well as the needs-based mixing processes. In addition, the new hydraulic system had to be installed and put into operation while production was running. Bosch Rexroth met these complex requirements with a tailor-made concept, took over the project planning and delivered, among other things, nine radial piston units from the Hägglunds AMX series for the slow-running high-torque reactors. These are much more compact and powerful compared to the previous solution. Apart from this, the oil supply for all 23 drives was replaced by new compact power units, with all high-pressure modules being operated with speed-controlled pumps.
One pump unit on each of the two central feed units is designed to be redundant. Since one of the two engine rooms is located in an EX zone, the compact power units installed there were realized in ATEX design. Rexroth frequency converters are used to precisely control the variable-speed hydraulic drives. Certified Excellence Partner Hydrobar provided the correct pipework for the plant and ensures the maintenance.
From Stahl’s point of view, the engineered-to-order project was a total success. Bosch Rexroth and the partners commissioned for the various trades were able to replace the hydraulic motors and variable-speed drives in just five months. “After preparing the pipework and electrics, including frequency converters, the relevant agitator was separated from the existing constant pressure network during the production-free period at the weekend,” says project manager Forcadell. “The modernized agitators were mostly put back into operation after three days.”
Bosch Rexroth also supported the assembly team as required with the installation of the new hydraulic motors and compact power units to ensure completion on time. “Despite its complexity, the project was implemented very quickly, especially on the control side. The pipework by Hydrobar was exemplary. Each plant was very well prepared, tested, and handed over ready for operation faster and faster. The last six drives were replaced within a week.”
From this control cabinet, the converters control the variable-speed driven Rexroth compact power units to supply the hydraulic motors with fluid. (Image source: Stahl)
The planned energy savings were also achieved to their full potential. “Bosch Rexroth’s multi-technology project was another milestone in our ESG roadmap,” says Alfieri. “The actual saving compared to the old constant pressure system is 60 percent, which means that the entire plant consumes 15 percent less power. The variable-speed approach to needs-based power supply keeps absolute power consumption at a consistently low level. Even with high utilization of the agitators, no fluctuations occur, so process reliability is continuously guaranteed.”
“Since the modern control system provides exactly the required power for each process step, we can keep the mixing conditions under control at all times,” adds project manager Forcadell. “As a result, we benefit from high reproducibility of the manufacturing process and constant product quality, with optimum energy efficiency.” Forcadell is also satisfied with the stability. “The dimensions of the compact power units with a redundant pump are just right. There has not been any downtime to date.”
Lightweight and powerful: the new Hägglunds AMX radial piston motor (right) is significantly more compact than the previous hydraulic motor (left).(Image source: Stahl)
Thanks to the new digital control of the hydraulic drives, Stahl now has a wealth of digital information available to analyze and document manufacturing processes. “We are currently setting up a process control system to visualize all parameters,” explains Alfieri. “This will make personal knowledge transferable. The information gained about certain settings and rapid error analyses simplify manufacturing in the long term.”
Thanks to the digitally controlled hydraulics from Bosch Rexroth, Stahl can now optimize the process quality specifically using the speed. A welcome side effect of the modernization is also the significantly quieter operation of the new Hägglunds hydraulic motors and the compact power units in the engine rooms. If the connected agitator does not need any power, the responsible high-pressure power unit is completely switched off. In the central service unit, feed pumps are automatically switched on as required. This standby operation reduces both the noise level and the energy requirement.
Following the successful modernization of the hydraulic drives, a new era has dawned for those responsible for production at Stahl’s Leinfelden location. “The sustainability and digitalization project has increased stability and process transparency in the area of high-performance coatings in the long term,” concludes Alfieri. “It was not an easy project, but the performance and collaboration between Bosch Rexroth and the partners involved was excellent. All requirements were met within the planned time and budget.”