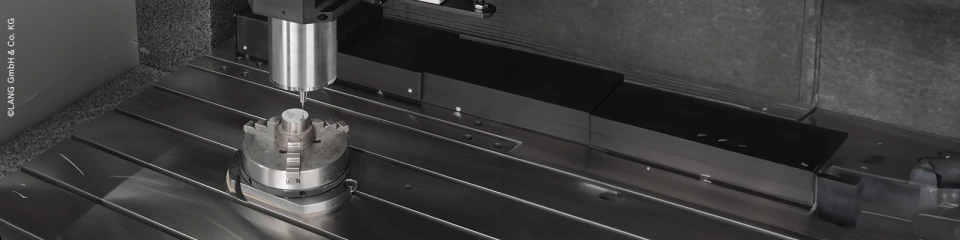
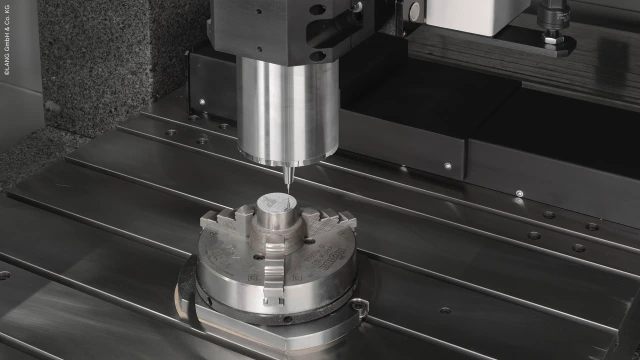
Industries
OverviewService
OverviewProduct groups
OverviewEngineering
OvervieweConfigurators and Tools
OverviewLANG engraving machines mill the finest structures into embossing dies for coins, toys, and huge vehicle tires. How does the hidden champion improve its competitive position for the long term? With, among other things, the integrated measuring system IMS, electromechanical cylinders EMC and many other Rexroth components from linear and automation technology.
For thousands of years, people have embossed objects to make them unmistakable and forgery-proof. To create the intricate structures on the dies of modern coins, car tires or toys, the highest precision is required – from the linear motion technology as well as from the associated drives and controls.
Established over 50 years ago in Hüttenberg, Hesse, the machine tool manufacturer LANG GmbH & Co. KG is an expert in the precision machining of stamping and embossing dies and is considered the global market leader in many areas. In addition to the automotive, coin and toy industries, LANG precision machines can also be found in wafer production, microscopy and the printing and packaging industries.
Some milling bits measure just three hundredths of a millimeter and are fed in the hundredth of a millimeter range for fine machining. The precision requirements for the linear, drive and control technology used are correspondingly high. The more that comes from a single source, the better, says Head of Design Marcus Boller:
LANG also uses ball and roller rail systems in combination with Rexroth linear motors as further components from the extensive Rexroth range. For example, in the Impala 400SL milling machine series, which is primarily used in the coin and miniature sector, where it achieves repeat accuracies in the µm range.
The fact that Bosch Rexroth is also deeply involved in the development pays off in the selection, design and configuration of the drives and motors, among other things. Because maximum precision can only be achieved if the mass inertia ratios are exactly right, emphasizes Marcus Boller. The finely tuned linear motion technology portfolio and the open and honest exchange make it easy to find the optimum solution for every application.
In addition to commercial aspects and delivery quality, the extended cooperation with Bosch Rexroth has also improved product quality over the long term. “The guides are so robust that they can remain in use for decades,” says the design manager. “It is also important to us that the supply of spare parts is guaranteed and that even outdated drive technology can be repaired for a long time to come.”
LANG has now equipped almost all of its machine series with linear guides and drive packages from Bosch Rexroth. On the control side, Marcus Boller appreciates the open interfaces that allow the self-programmed control software to intervene as deeply as possible. “Here too, we find good solutions in Bosch Rexroth’s comprehensive automation portfolio to further consolidate and expand our market position.”
Author: Thomas Ils
Position: Account Development Manager Central Europe Sales Linear Motion Technology, Bosch Rexroth AG