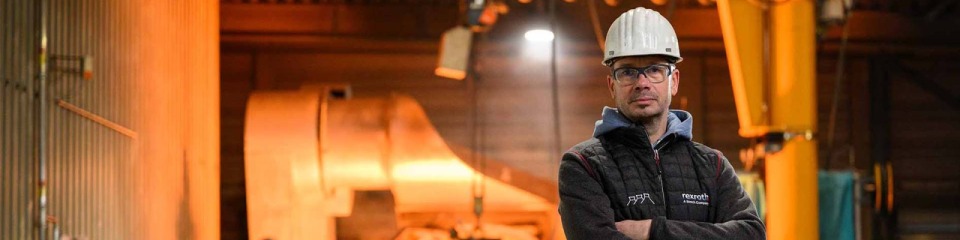
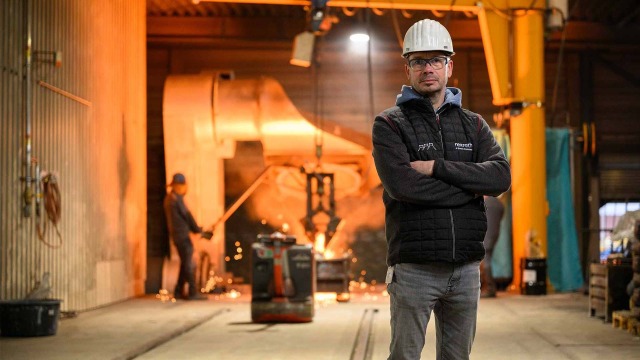
En Bosch Rexroth, buscamos constantemente formas de ahorrar energía. Descubra las innovaciones más recientes que hemos implementado en nuestras instalaciones en todo el mundo y que demuestran cómo, con un pensamiento creativo y un análisis cuidadoso, es posible contribuir a un mayor rendimiento energético.
Nuevas formas de enfriamiento
En la instalación de Lohr, en Alemania, las piezas de fundición hidráulicas se producen en varios grados diferentes de fundición. Una parte de este proceso de producción implica un tratamiento térmico especial conocido como “recocido”, donde las piezas fundidas se calientan a más de 900 °C y luego se enfrían de acuerdo con especificaciones definidas con precisión.
En el recocido se utiliza una enorme cantidad de energía, pero recientemente nuestros expertos han encontrado una manera más eficiente energéticamente: reemplazar el recocido del proceso por un enfriamiento lento.
Nuestro nuevo centro de enfriamiento nos permite eliminar el proceso de recocido, ayudándonos a reducir las emisiones de dióxido de carbono de nuestra fundición en más de 2500 toneladas al año. Esta innovación ejerce un impacto directo en la huella de carbono de nuestros productos.
(Derechos de imagen: Bosch Rexroth)
Reducción del consumo energético mediante la modernización del proceso de fusión
También hemos instalado nuestro tercer nuevo horno de fusión de frecuencia media en nuestra planta fundidora de Lohr. El nuevo horno cuenta con tecnología de fusión de última generación, donde cada elemento está diseñado para lograr un mayor rendimiento energético. De esta forma, hemos logrado reemplazar los tres hornos existentes por este nuevo.
Al digitalizar y automatizar los procesos de fusión, reestructurar el flujo de materiales y reducir el transporte de hierro y, por tanto, la pérdida de temperatura resultante, reducimos aún más nuestro consumo de energía. La nueva configuración de nuestro taller de fusión nos permite ahorrar hasta 2,9 GWh de energía eléctrica al año.
(Derechos de imagen: Bosch Rexroth)
Cambio al enfriamiento central por agua
Los sistemas de refrigeración por compresión son una parte clave del proceso de producción de componentes hidráulicos en nuestra instalación de Pekín. Funcionan de manera similar a los refrigeradores o acondicionadores de aire, que emiten aire caliente durante el funcionamiento del sistema. El aire caliente debe eliminarse a través del sistema de ventilación, lo que implica un alto consumo energético.
Nuestro equipo analizó cómo podía mejorar su gestión energética y se centró en la red de agua fría existente en la instalación, que ya se utilizaba para enfriar otras máquinas y procesos en producción. Descubrieron que el rendimiento energético podría mejorarse significativamente utilizando esta red de agua fría existente para enfriar las máquinas herramienta instaladas. Los sistemas de refrigeración por compresión podrían ser reemplazados por un intercambiador de calor conectado a la red de agua fría.
Lo implementamos en la primera fase, donde se convirtieron cinco centros de mecanizado, logrando una reducción del consumo energético para el enfriamiento en más del 80 % en comparación con la solución descentralizada, equivalente a un ahorro anual de aproximadamente 85 000 kWh.
(Derechos de imagen: Bosch Rexroth)
Producción de placas de circuito: ahorro de energía con radiación UV
En la planta de producción de placas de circuitos en nuestra instalación de Xi'an, China, las resinas sintéticas ahora se curan sin calor mediante el uso de rayos UV, lo que mejora significativamente las capacidades de ahorro de energía de la instalación.
Durante el proceso de producción, las placas de circuitos impresos (PCB) se ensamblan mecánicamente con componentes electrónicos y se sueldan. Después de las pruebas funcionales, la placa de circuitos impresos ensamblada (PCBA) se recubre con una pintura para proteger la electrónica de las influencias ambientales externas. Esto la hace apta para su uso en aplicaciones industriales.
Hasta hace poco, este recubrimiento se secaba con temperaturas de aproximadamente 100 °C durante 15-20 minutos, antes de que los PCBA tuvieran que enfriarse durante dos horas. Pero al usar la tecnología UV, el equipo de producción podría causar una reacción química en cuestión de segundos, ahorrando más del 80 % por PCB en uso de energía en comparación con el proceso anterior, y reduciendo así el tiempo de secado en aproximadamente el 90 %. Pero, además, el proceso permite aplicar un recubrimiento de pintura más grueso, lo que supone una mayor protección y una mejor calidad de las placas de circuitos fabricadas.
(Derechos de imagen: Bosch Rexroth)
Leo Pototzky
Director de Sostenibilidad Operacional