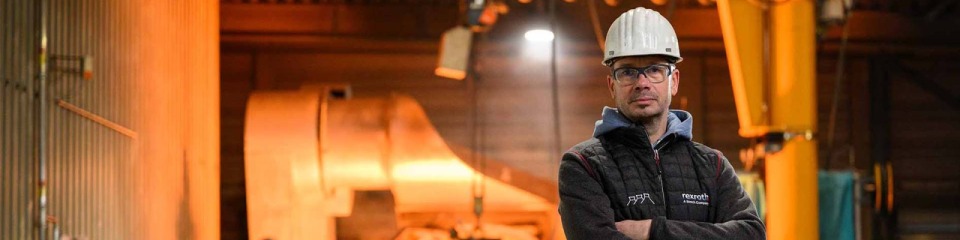
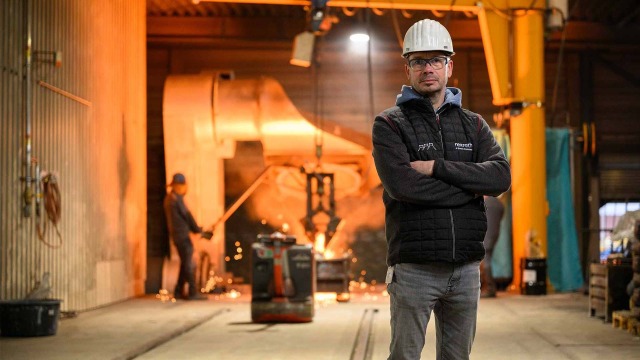
På Bosch Rexroth letar vi ständigt efter sätt att spara energi. Upptäck några av de senaste innovationerna som vi har implementerat i våra fabriker världen över – som visar hur det är möjligt att genom kreativt tänkande och noggrann analys bidra till ökad energieffektivitet.
Nya sätt att kyla ner
I Lohrfabriken i Tyskland tillverkas gjutjärnsprodukter av hydraulikgjutjärn i flera olika kvaliteter. En del av denna produktionsprocess innebär en särskild värmebehandling som kallas glödgning, där gjutgodset upphettas till över 900 °C och sedan kyls ned enligt exakt definierade specifikationer.
En enorm mängd energi används till glödgning, men nyligen har våra experter hittat ett mer energieffektivt sätt – ersätta glödgning från processen genom att sakta ner kylningen.
Vårt nya kylhus gör det möjligt att avskaffa glödgningsprocessen, vilket hjälper oss att minska koldioxidutsläppen från vårt gjuteri med mer än 2500 ton per år. Detta har en direkt effekt på våra produkters koldioxidavtryck.
(Bild till höger: Bosch Rexroth)
Minska energianvändningen genom modernisering av smältningsprocessen
Vi har dessutom installerat vår tredje nya medelfrekventa smältugn i vårt gjuteri i Lohr. Den nya ugnen har toppmodern smältteknik, där allt är utformat för ökad energieffektivitet. Detta gör det möjligt att ersätta tre befintliga ugnar med denna nya ugn.
Genom att digitalisera och automatisera smältprocesserna, omstrukturera materialflödet och minska järntransporten – och därmed den resulterande temperaturförlusten – minskar vi vår energiförbrukning ytterligare. Det nya upplägget i vårt smältverk gör att vi kan spara upp till 2,9 GWh elektrisk energi per år.
(Bild till höger: Bosch Rexroth)
Byte till central vattenkylning
Kompressionskylsystem är en viktig del av produktionsprocessen för hydrauliska komponenter i vår fabrik i Peking. Dessa fungerar på liknande sätt som kylskåp eller luftkonditioneringsapparater, med varm luft som avges när systemet är i gång. Den varma luften måste ledas bort via ventilationssystemet vilket innebär en hög energiförbrukning.
Vårt team undersökte hur de kunde förbättra sin energihantering och utnyttjade det befintliga kallvattennätet i fabriken, som redan används för att kyla andra maskiner och produktionsprocesser. De fann att energieffektiviteten kunde förbättras avsevärt genom att använda detta befintliga kallvattennät för att kyla ned installerade verktygsmaskiner. Kompressionskylsystemen skulle kunna ersättas med en värmeväxlare som är ansluten till kallvattennätet.
Vi lanserade detta i den första fasen, där fem bearbetningscenter byggdes om, vilket ledde till en minskad energiförbrukning för kylning med över 80 % jämfört med den decentraliserade lösningen – motsvarande en årlig besparing på cirka 85 000 kWh.
(Bild till höger: Bosch Rexroth)
Kretskortsproduktion: spara energi med UV-strålning
Vid produktionsanläggningen för kretskort i vår Xi’an-fabrik i Kina härdas syntetiska hartser nu utan värme genom att använda UV-strålar, vilket avsevärt förbättrar fabrikens möjligheter att spara energi.
Under produktionsprocessen monteras kretskort (PCB) mekaniskt med elektronikkomponenter och lödas. Efter funktionstester beläggs det monterade kretskortet (PCBA) med en färg för att skydda elektroniken från yttre miljöpåverkan. Detta gör den lämplig för användning i industriella applikationer.
Tills nyligen torkades denna beläggning i 15–20 minuter vid en temperatur på ca 100 °C innan kretskorten skulle svalna i två timmar. Genom att använda UV-teknik kunde produktionsteamet dock åstadkomma en kemisk reaktion inom några sekunder, vilket sparar över 80 % per PCB i energianvändning jämfört med den tidigare processen och minskar torktiden med cirka 90 %. Processen möjliggör dessutom en tjockare färgbeläggning vilket innebär högre skydd och bättre kvalitet av de producerade kretskorten.
(Bild till höger: Bosch Rexroth)
Leo Pototzky
Direktör, operativ hållbarhet